Manually inspecting aircraft parts with depth gages can be time consuming, encouraging many producers to opt for faster, more automated processes. So, when military helicopter manufacturer AgustaWestland needed to slash inspection times for panels on its Merlin helicopters, it chose the GapGun measurement device. AgustaWestland operators use Third Dimension’s handheld GapGun laser measurement system to quickly take detailed profile measurements of the depth of scratches on helicopter panels and aircraft gearbox components.
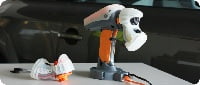
Maintenance, repair, and overhaul (MRO) inspection times for interior and exterior composite panels plummeted nearly 90%.
“They wanted something that would relieve the operators and provide some traceability compared with the manual gages,” Third Dimension’s Product Manager Paul Waterfall explains. Before using the device; if an operator noted a scratch, employees would remove that panel, bolt on a new one, and ship the damaged panel to a metrology lab to be measured for go or no-go. The panel would then be returned to join the group of spares until needed. The process could take up to eight months since they waited until they had a batch of panels to ship, resulting in huge costs. “This device has metrology lab quality but with handheld capabilities. It can be taken anywhere,” Waterfall says. “If the helicopter lands and someone says, ‘Well, I’m worried about this,’ you can take the GapGun to the helicopter, get a measurement within a couple of minutes, and go. You don’t need to remove and replace a panel.”
Quality assurance
The GapGun brings to the shop floor the accuracy and precision normally found only in a metrology lab. In 20 minutes, the device determines a part’s dimensional profile by taking a series of pictures of its surface. Operators can then establish whether scratch depths are within the required 0.15mm limit and verify whether the part needs to be repaired or replaced. “The data are also immediately transmitted to a back office so that you can keep a full record and traceability – by serial number, by operator,” Waterfall says. “That has really helped in understanding the manufacturing processes you’re using. You can pick up differences between different touch points easily.”
Optical measurements
A noncontact, automated laser measurement system, GapGun assesses the dimensional integrity or profile of a part without touching the surface. The device’s graphical user interface (GUI) guides users through the process, requiring only minimal training. GapGun uses laser triangulation technology to collect measurements. It projects a Laser Components line laser or stripe across the part’s surface to determine the measurable feature. “When we incorporated lasers from Laser Components, we got a more uniform, consistent, and reliable product, which sped up our manufacturing process,” Waterfall states. “It provides a very consistent focus.” Simultaneously, the integrated camera system takes images of the static laser stripe. Once the system measures the angle between the camera and the laser projection, an algorithm calculates the surface dimensions that the laser and camera scanned. These data generate a digital copy of the surface. Software produces a point cloud using image processing to convert the profile images into a series of points that extrapolate the feature’s shape. These points allow the system to analyze the measured surface. Because a laser is structured light, measurement data is highly reliable and can be used as a stable light source for data analysis. Features of the component’s profile measured include angle, radius, edge break, and scratch. The measurements are then recorded for statistical process control and traceability and transferred to a computer, allowing operators to determine any possible mistakes in the production line in real-time.
High-quality sensors
A camera view of a laser projected onto a surface allows operators to see gaps or changes in patterns. For example, a scratch may be shiny or green or brown in color. Operators measuring different surfaces need to control the laser intensity and the camera sensor. The GapGun Pro’s VChange sensor interface allows operators to quickly remove, swap, and reattach sensors. The sensors’ dynamic ranges extend from extremely bright surfaces, such as soft chrome, to the darkest paints of carbon surfaces. Changing laser intensity and controlling the camera achieves the necessary accuracy in measuring various challenging surface finishes. The device’s adjustable laser cap can shorten or split the laser line to measure complex features