What exactly are laser triangulation sensors and how can they be beneficial?
A laser triangulation sensor has the ability to take measurements through the reflected light from the target surface. Laser Triangulation sensors have been used for many years within metrology and continue to be of great benefit for many.
The method is called ‘triangulation’ because the sensor enclosure, the emitted laser and the reflected laser form a triangle. Whilst the technology behind it may not be new, it is very well suited to certain applications and provides a brilliant balance of cost vs. performance. Many industries benefit from laser triangulation sensors including OEM integration, Automotive, R&D testing, Aerospace and the White Goods Industry.
Benefits of Laser Triangulation Sensors:
- They are a mature technology that have been tested and refined over the years.
- They are robust and reliable
- The design can be made to be very compact, such as in the case of the GapGun Pro.
- Their compactness makes them ideally suited to both hand-held and automated applications in manufacturing.
- They are equally well suited to in-line and off-line applications
- It is a method of non-contact measurement, allowing measurements to be taken at a distance at high speeds without damage to the target.
Our Senior Product Manager, Clive Warren, recently completed a virtual presentation discussing laser triangulation sensors which you can take a look at below:
Types of Laser Triangulation Sensor:
There are typically two types of laser triangulation sensor. There is a ‘Point Sensor’. In this instance, the beam is projected as a spot onto the surface under test (SUT). The sensor then outputs the distance to the surface. In these configurations, the sensor is typically mounted in a fixed location. To obtain absolute distance measurement you would need to perform a careful calibration of the whole set up before the measurement data can be used.
The second way that a laser triangulation sensor may be configured is as a ‘Line Sensor’. This is where the laser projects a continuous line of light across the SUT. It is worth noting that the projected line appears distorted when it reaches the image sensor. Analysis of that distorted image enables accurate reconstruction of the object shape, providing a 2D profile. You can achieve a 3D point cloud by moving the object perpendicular to the line. Once again, calibration is essential to ensure achieving accurate results from the sensor.
The GapGun Pro2 – A SMART Laser Triangulation Sensor
An example of a SMART laser triangulation sensor would be the GapGun Pro2. This device is an all in one fully self-contained device based on laser triangulation technology. As a result of the compact nature of the device, it has been possible to include:
- The CPU (Central Processing Unit)
- Application Software
- Human Device Interface (HDI / GUI)
- Data storage
- Communications Hardware
All of this is stored in one compact, robust unit that can be deployed either by hand or in automated applications. These sensors can be used on a variety of different measurement applications such as: Gaps, Flushes, Chamfers, Edges, Radii, Angles, Seals, Steps, Mismatches and more.
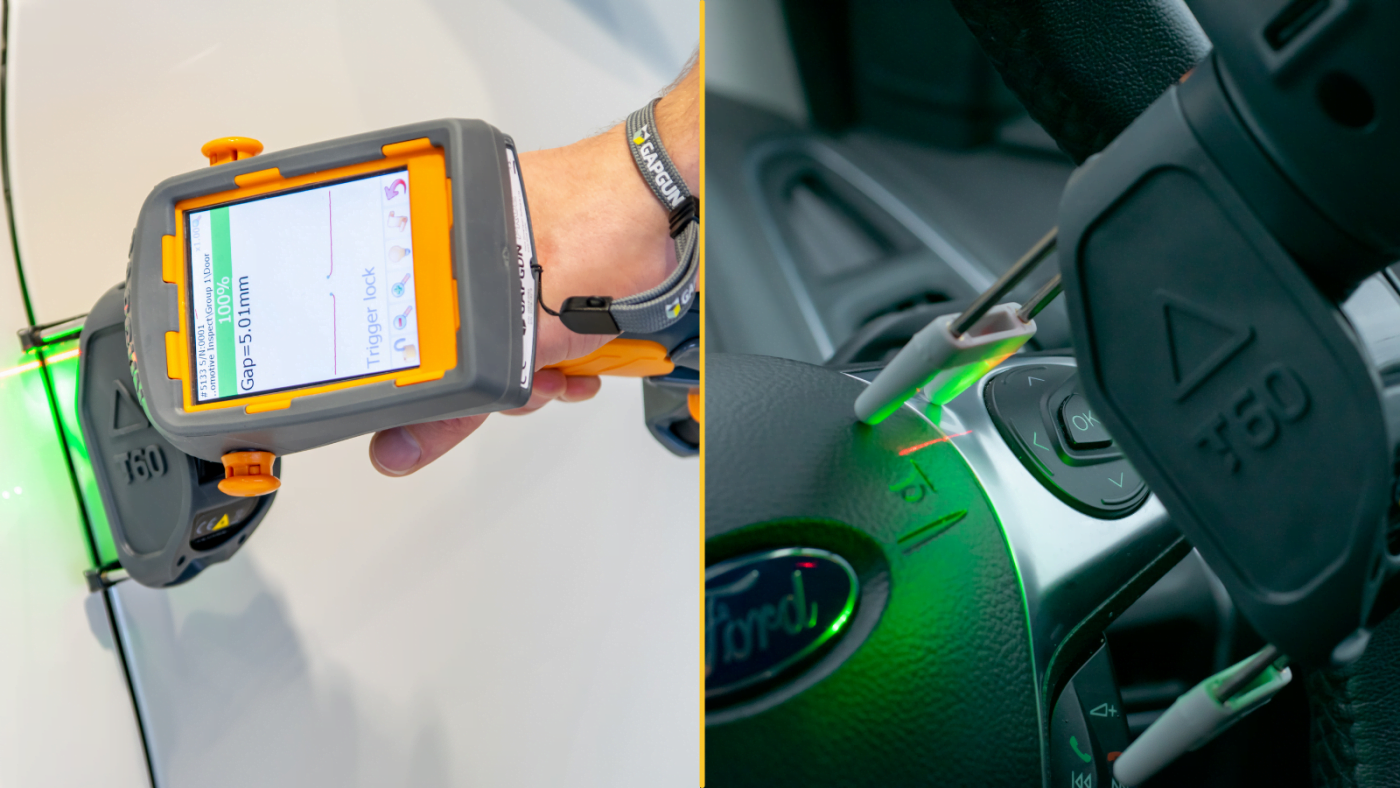
Environmental Challenges of Laser Triangulation Sensors:
- Temperature – The laser, lens and image sensor all need to be a fixed relation away from each other. If temperature impacts on this, it can have a dramatic influence on the measurements achieved; Therefore, careful design is required and use of materials with a low chance of expansion/contraction helps reduce effects of temperature.
- Lighting – Ambient lighting, such as sunlight or shadows can all effect the light that is impinging on the image sensor. This problem is largely solved by deploying filters that only allow the specific wavelength of the laser to pass through, essentially blocking all other light forms allowing for reliable measurements to be taken.
- Spectral Transmission – This is the transmission of light through a material. For example, if you wanted to measure a clear material, such as automotive glass or the protective cover on a headlight, you would have to choose a laser with an appropriate wavelength.
To find out more about metrology and how Third Dimension’s non-contact, precision profile measurement solutions can benefit your business, contact us here.